Continuous Stirred Tank Reactors Scale Down
The continuous stirred-tank reactor is known as CSTR, or commonly the stirred tank reactor (STR), and it is similar to the batch reactor. The main difference is that preparation must be made for continuous flow of ingredients in the reactor by gravity or forced-circulation flow using a pump for the stirred tank reactor. The continuous stirred tank reactor is sometimes named a BMR or back-mixed flow reactor.
Similar to a batch reactor, an agitator is intentionally added in a continuous stirred-tank reactor to fully disperse the reactants into a reaction compound immediately after they enter the tank. The product flow is continuously drawn off from the tank. The output reaction mixture is expected to be a well-mixed product.
What is a Chemical Reactor?
A chemical reactor is a confined volume where chemical reactions take place. In chemical engineering, it is frequently known as a process vessel employed to carry out a chemical reaction. In chemical process analysis, it is one of the classic unit operations. The design of a chemical reactor includes multiple aspects of chemical engineering.
Engineers study reactors to raise the net present value for the presented reaction. They ensure that the reaction continues with the highest efficiency towards the wanted output product, providing the highest yield of the product while demanding the least amount of capital cost to purchase and operate. Regular operating expenses are energy removal, energy input, raw material costs, labor, etc. Energy conversions can come in pumping to increase pressure, heating or cooling, frictional pressure loss, or agitation. For analyzing and designing these systems, you should know chemical kinetics.
Types of Chemical Reactors
The most basic types of chemical reactors are tanks and pipes or tubes. The reactants mix in the whole volume in tanks, while pipes or tubes are for plug flow reactors and laminar flow reactors.
Both types can be chosen as batch reactors or continuous reactors. Either may contain one or more solids (reagents, catalysts, or inert materials). Still, the reagents and outcomes are typically fluids (liquids or gases). Reactors are typically run at a steady state in continuous processes. In contrast, reactors in batch processes are necessarily worked in a transient state. When a reactor is starting operation, it is in a transient state either for the first time or after a shutdown, so key process variables vary with time.
We have three idealized types used to determine the most important variables of different chemical reactors:
- Continuous Stirred-Tank Reactor Model (CSTR)
- Batch reactor model,
- Plug Flow Reactor (PFR) model .
We can model many practical reactors by using a combination of these basic types.
Key process parameters include:
- Residence time (τ, lower case Greek tau)
- Temperature (T)
- Pressure (P)
- Volume (V)
- Heat transfer coefficients (h, U)
- Concentrations of chemical species (C1, C2, C3, … Cn)
A tubular reactor is usually a packed bed. In this example, the tube or channel comprises particles or pellets, regularly a solid catalyst. The fluid reactants, the gas or liquid phase, are pumped over the catalyst bed. A chemical reactor can also be a type of fluidised bed.
Chemical reactions happening in a reactor can be exothermic, giving off heat, or endothermic, absorbing heat. A tank reactor may possess cooling or heating coils (tubes) or a jacket wrapped around the exterior of its vessel wall to heat up or cool down the contents. On the other hand, we can design tubular reactors similar toheat exchangers if the reaction is greatly exothermic, or like furnaces, if the reaction is greatly endothermic.
What is the Continuous Stirred-Tank Reactor?
The continuous stirred-tank reactor (CSTR), also name amixed flow reactor(MFR),vat-or back mix reactor, or acontinuous-flow stirred-tank reactor(CFSTR), is one types of chemical reactor in environmental engineering and chemical engineering. A CSTR usually refers to a class utilized to estimate the critical unit running variables when employing a continuous agitated-tank reactor to have a specified output. The mathematical model is valid for all fluids, same as liquids, gases, and slurries.
A continuous stirred-tank reactor is typically used for homogeneous liquid-phase reactions. For the laboratory applications, we may also use it for a gas-phase reaction for temporary measurements, especially for a catalysed reaction. The continuous stirred-tank reactor is accepted for a gas-liquid reaction when gas has a reaction with a liquid phase, and the gas molecules transfer from the gas into the liquid phase. The gas is introduced under the impeller, and the Gas-Liquid reaction will happen in a later section.
Because of slow reaction rates in a continuous stirred-tank reactor, the reactor volumes usually are large. A CSTR-type reaction process is usually carried out in a series of reactors to provide higher conversions, named cascades of CSTR.
Continuous stirred-tank reactors have the following characteristics:
- Continuous flow passes through a CSTR, both output and input streams. But not certainly at equal rates.
- The mass of the system inside a CSTR is not necessarily steady.
- The fluid is perfectly mixed inside a CSTR. Hence, its properties are consistent at any time because of adequate stirring.
- The flow in the system may not necessarily have a constant density. The density of the inlet flow may vary among the process to reach the exit and have a different density output stream.
- The system may work at unsteady-state or steady-state.
- We may provide some kinds of heat transfer equipment for temperature control.
There are several significant consequences of the model explained above, as presented below:
- The fluid inside the continuous stirred-tank reactor is uniformly mixed, and components of fluid are uniformly dispersed. As a result, all fluid particles have an equal possibility of leaving the reactor with the output flow at any time.
- As an outcome of the above item, the output stream holds the properties same as the fluid inside the reactor.
- Consequently, there is a step-change in any property of the system that changes within the inlet to outlet.
- There are two extremes: first, fluid flowing directly from inlet to outlet in a short time (t). Second: fluid being caught up in loops cycling many times by the stirring action in a long time (t).
- For steady-state flow, the average residence time of fluid inside the tank is the ratio of the total reactor volume to the volumetric steady-state flow rate of fluid at the outlet of the reactor.
- For steady-state flow, space-time is the ratio of the total reactor volume to the steady-state flow rate for the feed at inlet states.
- For steady-state multi-stage operation, every stage of a CSTR is stable (uniform concentration, temperature, etc.), independent of time.
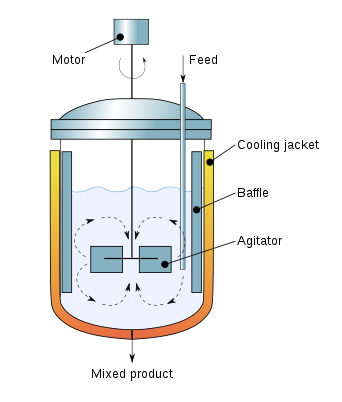
Parts of a Continuous Stirred-Tank Reactor
CSTRs consist of a tank, regularly with a constant volume, and stirring equipment to mix reactants. Feed and outlet pipes are present to enter reactants and discharge products. The figure below shows a cross-section of a CSTR and the interior part of that.
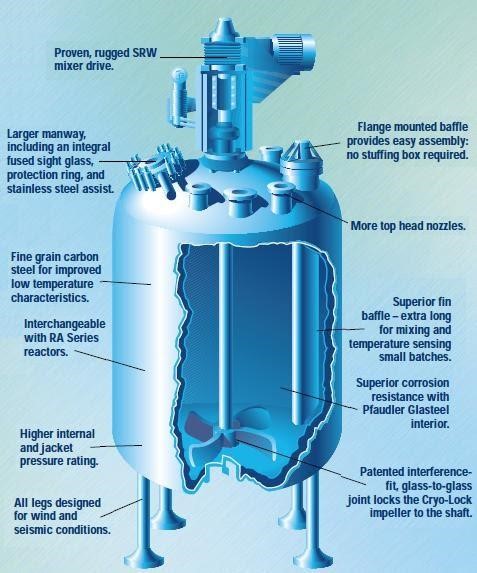
We call the stirring blades agitators, and they are prepared in the tank to mix the reactants. Here some of the various agitators are presented that are used inside CSTRs.
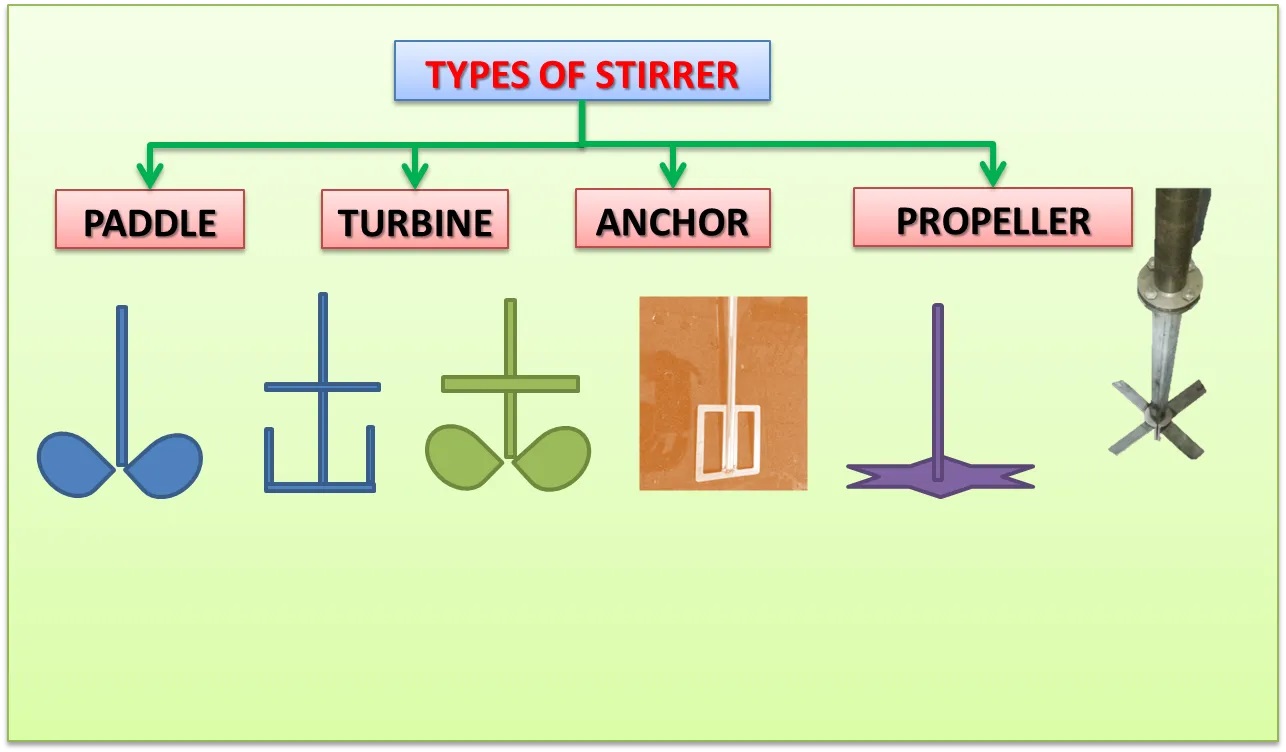
A CSTR can also operate as a loop reactor if a heated, pressurized fluid is introduced into the system to help the stirring. It provides higher heat and mass transfer rates, including easy maintenance because of not having agitators.
A cell culture reactor is presented below. An exact amount of cells are set on the fibrous-bed basket. A rich nutrient medium is continuously supplied into the reactor, and outputs are harvested. As the cells mature, they provide by-products, which are continually extracted from the reactor. The presented reactor has a pitched-blade impeller to mix the reactants continuously.
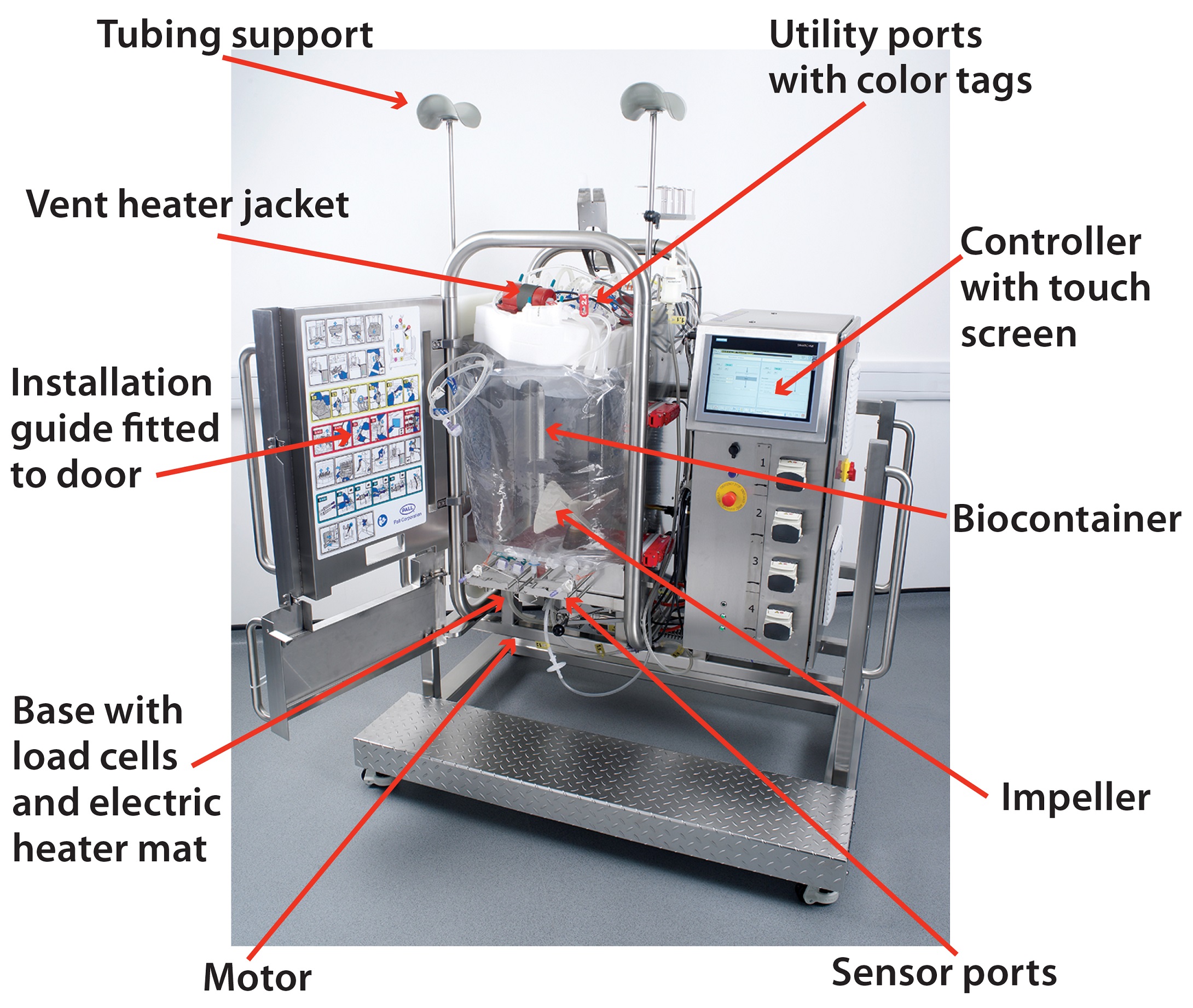
Modeling Continuous Stirred-tank Reactor
The performance of a CSTR is frequently approximated or modeled by an ideal CSTR, which considers perfect mixing. In a perfect reactor, reagents are uniformly and instantaneously mixed in the whole reactor upon entry. Consequently, the output combination is identical to the composition of the materials inside the reactor, which is a purpose of reaction rate and residence time.
The CSTR is the ideal limit of perfect mixing in reactor designs, which is the reverse side of a Plug Flow Reactor (PFR). Practically, we do not have an ideal reactor but instead, all fall somewhere between the mixing limits of a PFR and an ideal CSTR.
Ideal CSTR
Here we will model a continuous fluid flow including non-conservative chemical reactant (A) enters an ideal continuous stirred-tank reactor of volumeV.
Assumptions:
- Ideal or perfect mixing
- For steady-state we have \frac{dN_a}{dt}=0 , whereNA is the moles number of speciesA
- Fluid density is constant (almost valid for most liquids; also valid for gases if there is no net change for the number of moles or extreme temperature change)
- Closed boundaries
- nth-order reaction( r=k{C_{A}^{n}} ), where CA is the concentration of speciesA, k is the reaction rate constant, andn is the order of the reaction
- Isothermal process, or constant temperature, sok is constant.
- For the single, irreversible reaction:νA = −1
- All reactantA is reacted completely to provide products.
- N_A=C_AV
Integral mass balance for the number of molesNA in a reactor of volumeV gives:
[Net Accumulation of A] = [A in]-[A out]+[Net Generation of A]
\frac{dN_A}{dt}=F_{A_0}+F_A+V\upsilon _ar_a
where,
- FA is the molar flow rate of species A in the outlet
- FAo is the molar flow rate of species A in the inlet
- rA is the reaction rate
- vA is the stoichiometric coefficient
Using the equations of steady-state and νA = −1, simplifies the equations above to:
0=F_{A_0}+F_A+V r_a
The molar flow rates for species A can be rewritten based on the fluid flow rate (Q) and the concentration of A:
0=QC_{A_0}-QC_A-Vr_A
Now we can find rA by simplifying the equations:
r_A=\frac{Q}{V}(C_{A_0}-C_A)
r_A=\frac{1}{\tau }(C_{A_0}-C_A)
Where:
- \tau is the theoretical residence time ( \tau = \frac{Q}{V} )
- CAo is the concentration of species A in the inlet
- CA is the concentration of species A at the reactor or outlet
Residence time is the entire amount of time a discrete quantity of reagent mixed inside the reactor. For a perfect and ideal reactor, the theoretical residence time, \tau , can be calculated easily by dividing the reactor volume by the fluid flow rate.
Based on the order of the reaction,rA (the reaction rate) generally has a strong dependence on the concentration of speciesA and the rate constant in the reactor. A fundamental theory for modeling an ideal CSTR is uniformly mixing, indicating that the concentration inside the reactor is to the concentration at the outlet stream.
We can determine the rate constant by empirical reaction rate adjusted for temperature by employing the Arrhenius temperature dependence. Generally, as the temperature rises, so does the rate at which the reaction occurs.
The equations below are the concentration of speciesA at the outlet for an ideal CSTR. The outlet concentration and residence time values are significant design criteria in designing CSTRs for industrial applications. Outlet Concentration for an Ideal CSTR with different reaction order is presented below:
n=0\rightarrow C_A=C_{A_0}-k\tau
n=1\rightarrow C_A=\frac{C_{A_0}}{1+k\tau }
n=2\rightarrow C_A=\frac{-1+\sqrt{1+4k\tau C_{A_0}}}{2k\tau }
for n=3 we need an extra calculations
Residence Time Distribution
An ideal CSTR will show well-defined flow performance characterized by using the reactor's exit age distribution or residence time distribution. All fluid particles will not spend the same time in the reactor. The exit age distribution (E(t)) determines the probability that a specified fluid particle will spend time t within the reactor.
Furthermore, the cumulative age distribution (F(t)) provides the probability that a specified fluid particle has an exit age shorter than time t. One of the important disadvantages of the exit age distribution is that all the fluid particles will never exit the reactor. Based on the application, this can either be a drawback or an asset.
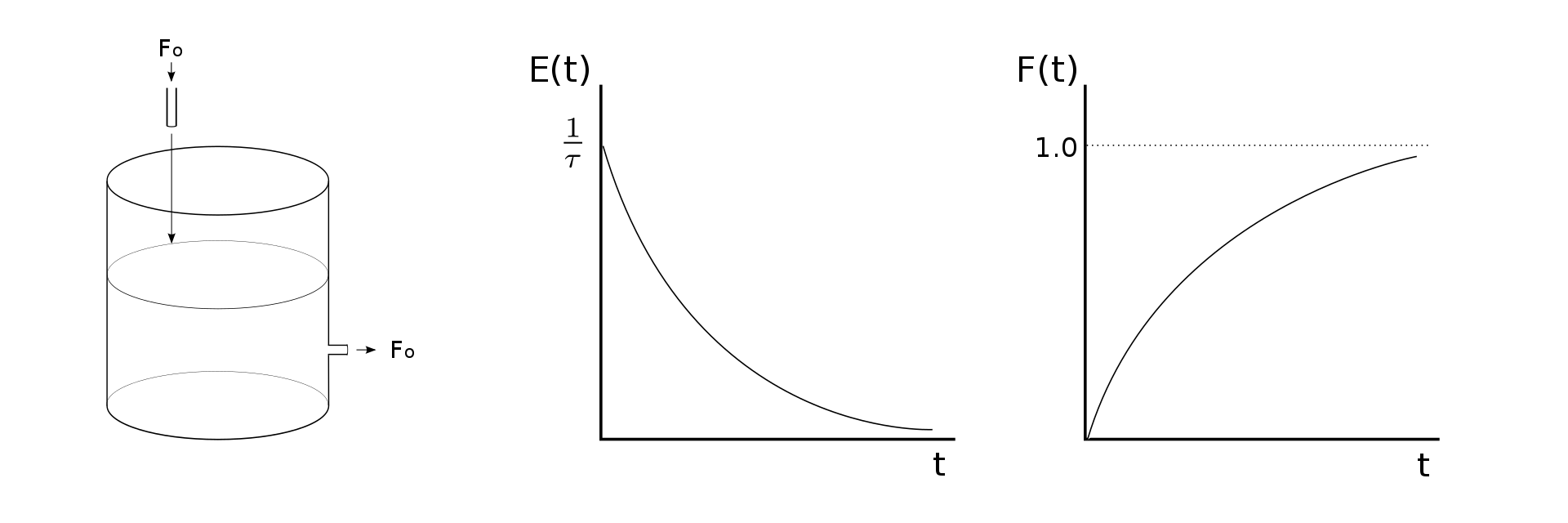
Non-ideal CSTR
The ideal CSTR design helps predict the outcome of constituents through a chemical or biological process, but CSTRs rarely show ideal performance in reality. The reactor hydraulics do not function ideally, or the process conditions do not follow the initial assumptions. Ideal mixing is a theoretical concept that is not possible in practice. However, if the residence time is 5-10 times the mixing time in engineering applications, the perfect mixing theory generally is true.
Non-ideal hydraulic performance is usually classified by either short-circuiting or dead space. These phenomena occur when one or some fluid spends less time inside a reactor compared to the theoretical residence time, \tau . The proximity of corners or baffles in a reactor frequently results in some dead zones where the fluid is inadequately mixed.
Similarly, a fluid jet in the reactor may cause short-circuiting, which means some of the flow exits the reactor faster than the bulk fluid. Suppose dead space or short-circuiting occurs in a CSTR. In that case, the appropriate chemical or biological reactions may not complete before the fluid exits the tank. Any deviation from perfect flow results in a change residence time diagram, which causes a difference from the ideal distribution.
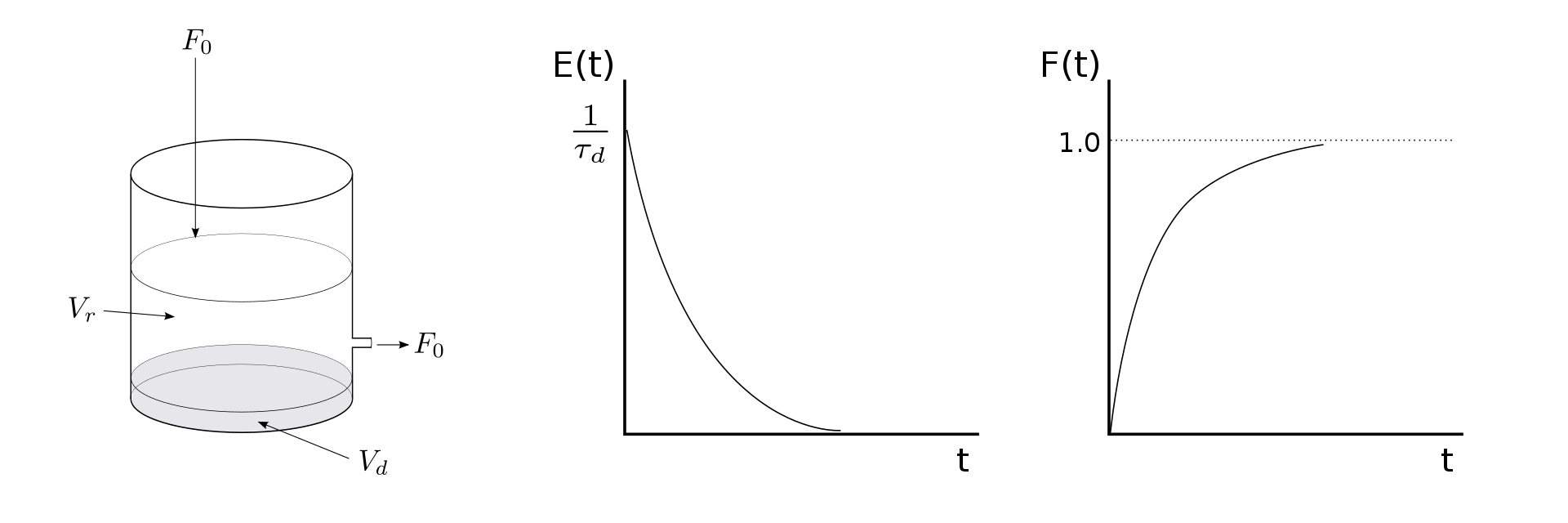
Non-Ideal Flow Modeling
Ideal flow reactors are rarely found in use, but they are valuable tools in modeling non-ideal flow reactors. We can achieve any flow regimes by modeling a reactor as a mixture of ideal CSTRs and plug flow reactors (PFRs) both in parallel or series. For instance, an endless series of ideal CSTRs is hydraulically equal to a perfect PFR. Reactor designs which are combining several CSTRs in series are usually termed tanks-in-series (TIS) models.
Additional dependent variables must be analysed for modeling systems that do not obey the theories of a single reaction and constant temperature. If we have an unsteady-state system, one differential equation or several coupled differential equations must be solved. The dispersion model considers deviations of the CSTR behavior. CSTRs are known to be systems that present complex behavior, same as limit cycles, steady-state multiplicity, and chaos.
Applications
CSTRs promote rapid dilution of reagents by mixing. Consequently, for non-zero-order reactions, the low concentration reagent in the reactor determines a low-efficiency CSTR at removing the reagent than a PFR with a similar residence time. So, CSTRs are usually larger than PFRs, and it is not appropriate for applications with limited space. However, an advantage of dilution in CSTRs is the strength of neutralising shocks in the system. The performance of CSTRs is less sensitive to fluctuations in the influent composition as opposed to PFRs. It is an ideal choice for many industrial applications:
Environmental engineering:
- Lagoon treatment for natural wastewater treatment systems.
- Wastewater treatment by activated sludge process.
- Anaerobic digesters in the wastewater for stabilization of biosolids.
- Treatment wetlands for stormwater and wastewater runoff.
Chemical engineering:
- Loop reactor for pharmaceutical production.
- Fermentation.
- Biogas production.
Usage Examples
Continuous stirred-tank reactors are most generally employed in industrial processing, essentially for homogeneous liquid-phase flow reactions with constant agitation. They may work in series or a battery. CSTRs are also essential equipment in the pharmaceutical industry function as a loop reactor.
A dimple jacketed pressure vessel can be used in cosmetics, oil and gas, chemicals and petrochemicals, pharmaceuticals, food, dairy, and beverage operations and can be designed based on the unique process system requirements. The figure below presents a dimple jacketed pressure vessel.
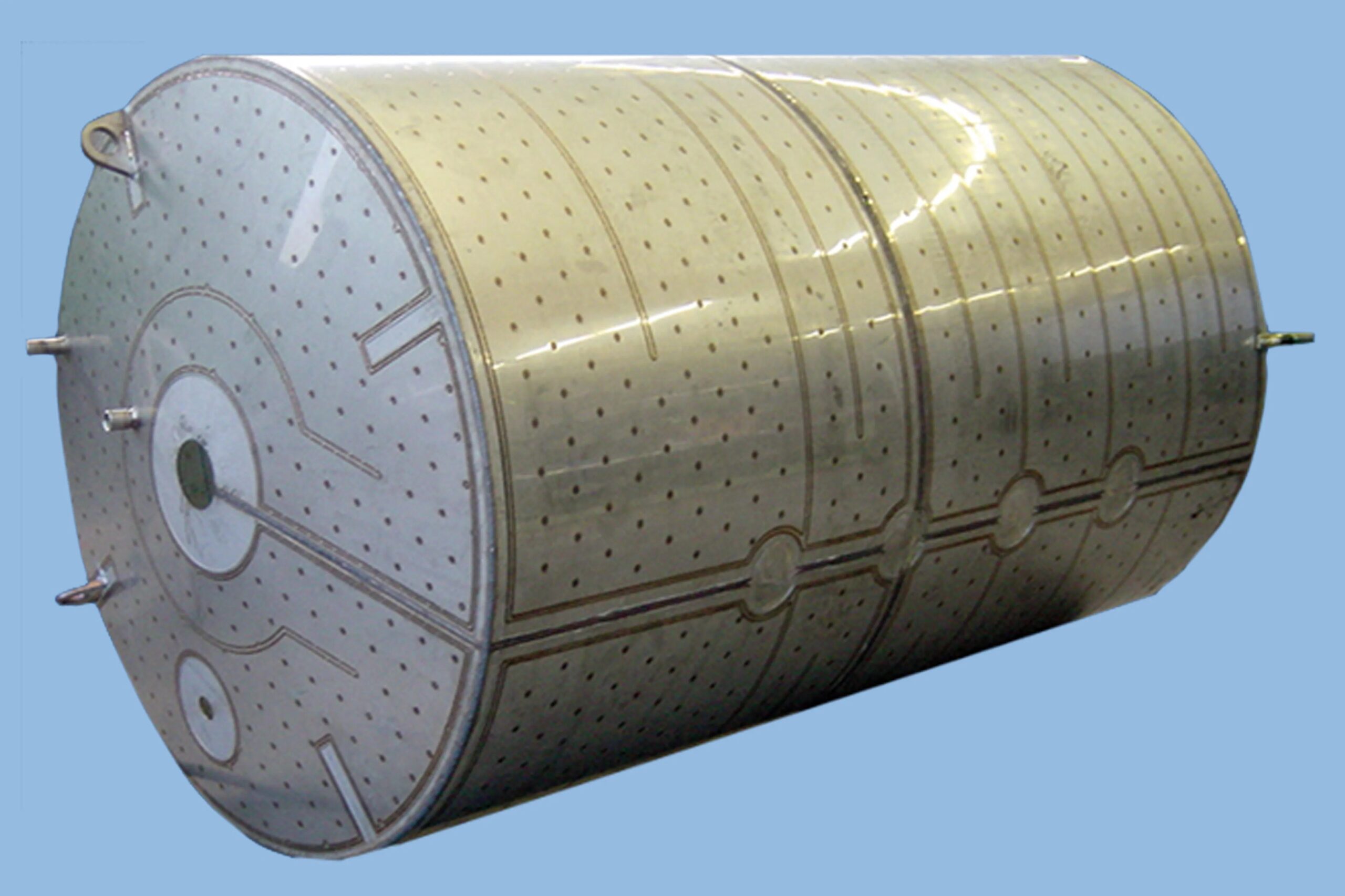
As discussed earlier, CSTRs can be used in biological processes for high-density cell culture in production or research. The vessels in this application are for single use.
The fermenter is another application of CSTRs for a biological catalyst to produce products. Microbes catalyze a reaction that breaks down larger molecular units into smaller products such as methanol, ethanol, or other hydrocarbons in a fermenter. We can remove vapor products from the top without separation. Also, liquid products can be extracted from the bottom, filtering and recovering the microbial media. Fermenters are such important equipment in many industries, such as wastewater treatment, brewing, pharmaceuticals, and hydrocarbon processing.
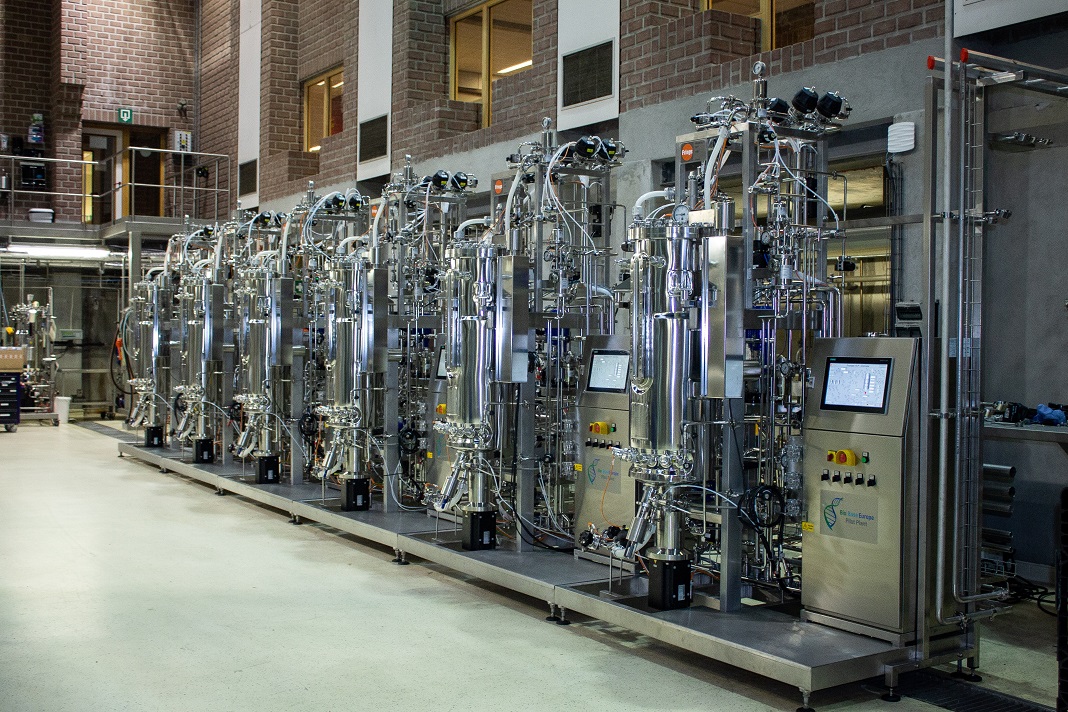
Advantages and Disadvantages
Advantages and disadvantages of CSTRs are presented below:
Advantages:
- Good temperature control
- Continuous operation
- Simplicity of construction
- Cheap reactor
- Easily adapts to two-phase runs
- Good control
- Easy to clean
- Low operating (labor) cost
- Interior parts are easily accessed
- Large capacity
Disadvantages:
- It has Size limitation because of motor size, weight, and shaft length.
- It needs shaft seals and bearings.
- It may have some dead zones.
- Reactants can bypass because of improperly positioned outlet.
- It has a poor conversion ratio.
Source: https://www.linquip.com/blog/what-is-a-continuous-stirred-tank-reactor/
0 Response to "Continuous Stirred Tank Reactors Scale Down"
Post a Comment